
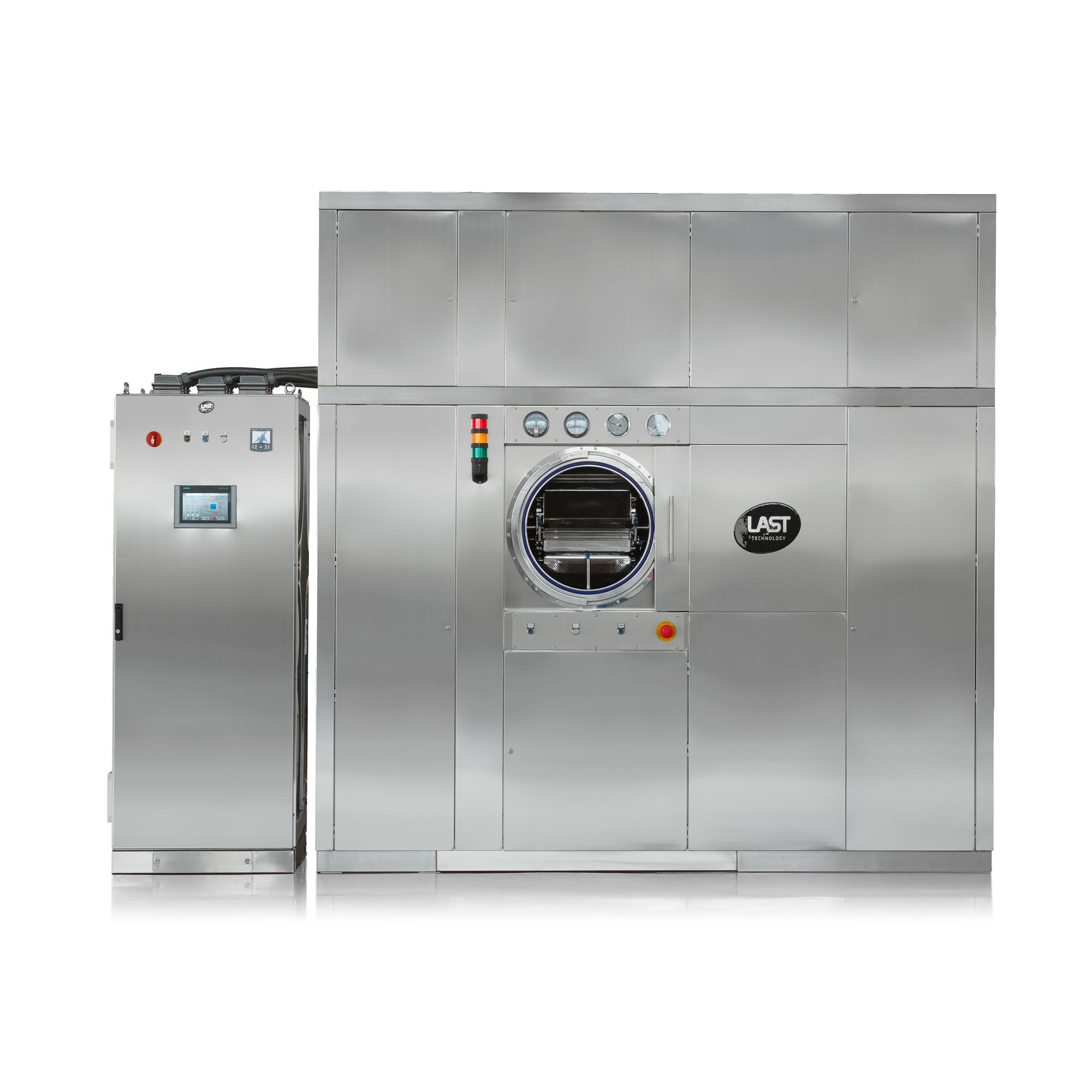
Predefined and “custom” programmes for every need. The equipment process is developed by our Automation Department, according to the current regulations/standards and the load type.
The main stages of the process are as follows:
- Pre-wash
- Extraction (if required)
- Wash (with or without cleaners)
- Rinse (the number of repetitions is definable)
- Silicone coating (if required)
- Sterilisation by means of saturated steam (the CPE model only)
- Drying
- Cooling
This equipment boasts various features that set it apart from the competition, namely its ability to separate the load into different compartments (hoppers/baskets) with uniform capacity. As a result, the following advantages can be obtained:
- No excessive build-up of material during the process phases.
- No mechanical stresses on the material.
- An optimised washing phase.
- Uniform silicone distribution.
- An optimised CIP phase.
- An optimised sterilisation phase.
- Well-dried material.
- High flexibility as far as product unloading methods are concerned.
- Double-walled circular chamber.
- Flat-type all-round cavity to uniformly and quickly heat the load.
- Two 1.5” tri-clamp ferrules are welded to the chamber for validation purposes (temperature uniformity mapping and pressure tests).
- The piping and air ducts are made entirely from 316L stainless steel with sanitary fittings (tri-clamp ferrules and hygienic flanges).
- Chamber with perfect drainage.
- The equipment body is supported by a base that evenly distributes the floor loads.
- All of the chambers internal surfaces are mechanically polished and then subjected to chemical degreasing, pickling and passivation treatments. Surface finish: ≤ 0.35 micron.
- The unloading-side door hopper has been designed to be completely sealed with the “bio-seal” clean chamber.
- Various fully automatic product unloading options.
cGMP Closure Processing Equipment
PHARMA DIVISION
cGMP Closure processing equipment description
The CPE and CPE-W closure processing equipment has been designed to fully process (from dirty to ready to be sterilised or ready to use) pharmaceutical closures, such as rubber caps, pistons and seals, plastic parts, aluminium caps and combi-seals, etc.
POROUS AND NON-POROUS
WATER + CLEANERS + SILICONE + SATURATED STEAM + AIR
20°C – 121°C
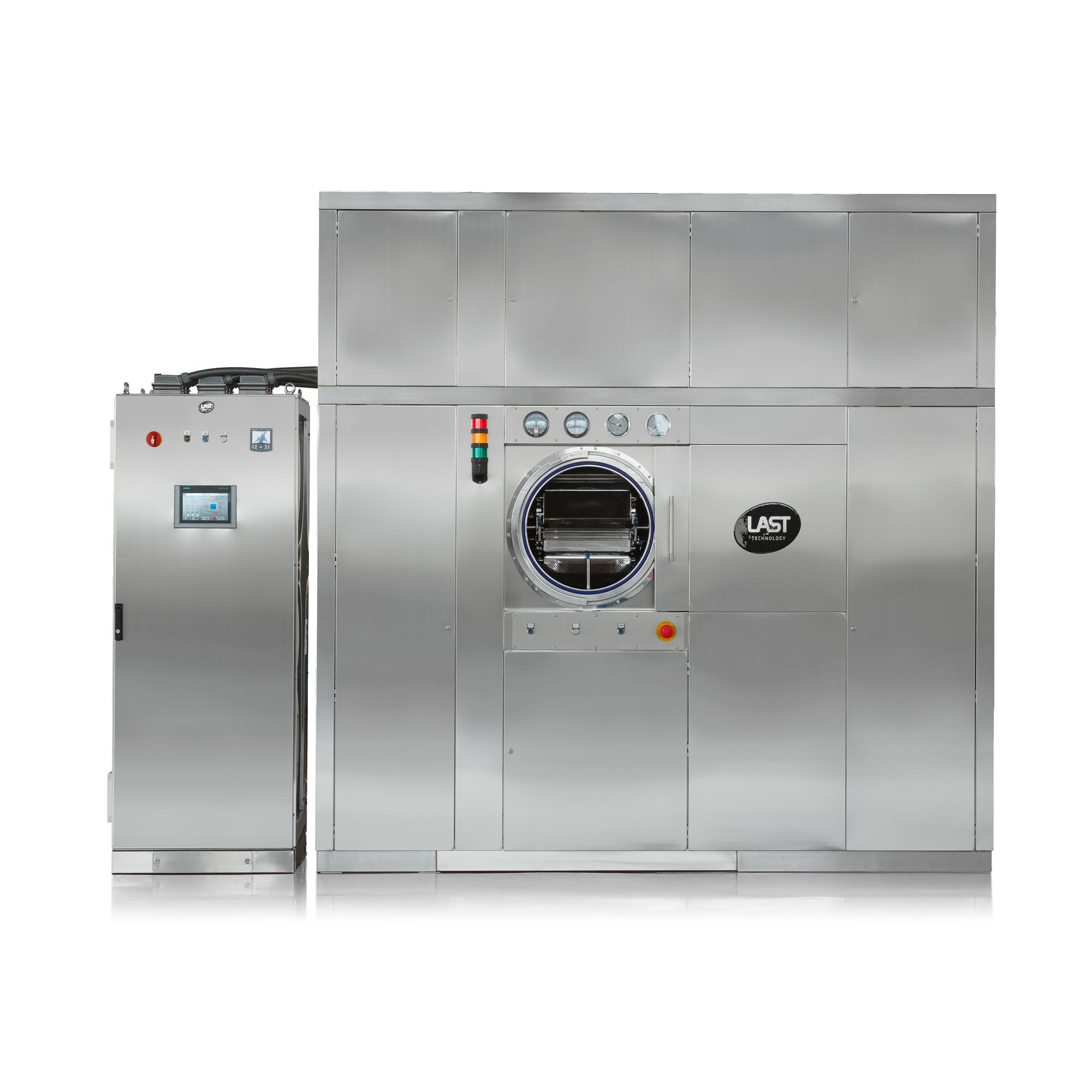
Predefined and “custom” programmes for every need. The equipment process is developed by our Automation Department, according to the current regulations/standards and the load type.
The main stages of the process are as follows:
- Pre-wash
- Extraction (if required)
- Wash (with or without cleaners)
- Rinse (the number of repetitions is definable)
- Silicone coating (if required)
- Sterilisation by means of saturated steam (the CPE model only)
- Drying
- Cooling
This equipment boasts various features that set it apart from the competition, namely its ability to separate the load into different compartments (hoppers/baskets) with uniform capacity. As a result, the following advantages can be obtained:
- No excessive build-up of material during the process phases.
- No mechanical stresses on the material.
- An optimised washing phase.
- Uniform silicone distribution.
- An optimised CIP phase.
- An optimised sterilisation phase.
- Well-dried material.
- High flexibility as far as product unloading methods are concerned.
- Double-walled circular chamber.
- Flat-type all-round cavity to uniformly and quickly heat the load.
- Two 1.5” tri-clamp ferrules are welded to the chamber for validation purposes (temperature uniformity mapping and pressure tests).
- The piping and air ducts are made entirely from 316L stainless steel with sanitary fittings (tri-clamp ferrules and hygienic flanges).
- Chamber with perfect drainage.
- The equipment body is supported by a base that evenly distributes the floor loads.
- All of the chambers internal surfaces are mechanically polished and then subjected to chemical degreasing, pickling and passivation treatments. Surface finish: ≤ 0.35 micron.
- The unloading-side door hopper has been designed to be completely sealed with the “bio-seal” clean chamber.
- Various fully automatic product unloading options.
cGMP Closure Processing Equipment
PHARMA DIVISION
cGMP Closure processing equipment description
The CPE and CPE-W closure processing equipment has been designed to fully process (from dirty to ready to be sterilised or ready to use) pharmaceutical closures, such as rubber caps, pistons and seals, plastic parts, aluminium caps and combi-seals, etc.
POROUS AND NON-POROUS
WATER + CLEANERS + SILICONE + SATURATED STEAM + AIR
20°C – 121°C
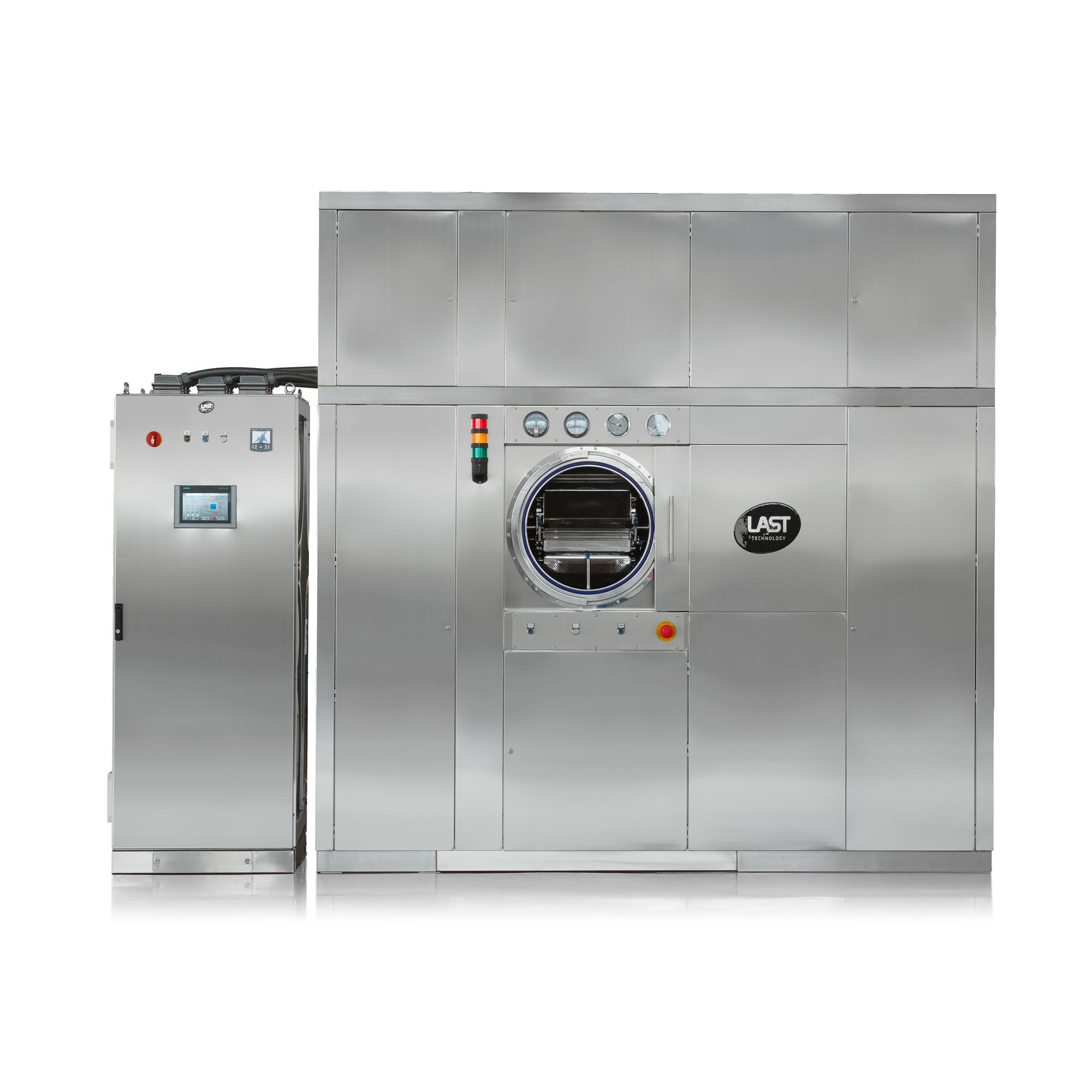
cGMP Closure Processing Equipment
PHARMA DIVISION
cGMP Closure processing equipment description
The CPE and CPE-W closure processing equipment has been designed to fully process (from dirty to ready to be sterilised or ready to use) pharmaceutical closures, such as rubber caps, pistons and seals, plastic parts, aluminium caps and combi-seals, etc.
20°C – 121°C
POROUS AND NON-POROUS
WATER + CLEANERS + SILICONE + SATURATED STEAM + AIR
Predefined and “custom” programmes for every need. The equipment process is developed by our Automation Department, according to the current regulations/standards and the load type.
The main stages of the process are as follows:
- Pre-wash
- Extraction (if required)
- Wash (with or without cleaners)
- Rinse (the number of repetitions is definable)
- Silicone coating (if required)
- Sterilisation by means of saturated steam (the CPE model only)
- Drying
- Cooling
This equipment boasts various features that set it apart from the competition, namely its ability to separate the load into different compartments (hoppers/baskets) with uniform capacity. As a result, the following advantages can be obtained:
- No excessive build-up of material during the process phases.
- No mechanical stresses on the material.
- An optimised washing phase.
- Uniform silicone distribution.
- An optimised CIP phase.
- An optimised sterilisation phase.
- Well-dried material.
- High flexibility as far as product unloading methods are concerned.
- Double-walled circular chamber.
- Flat-type all-round cavity to uniformly and quickly heat the load.
- Two 1.5” tri-clamp ferrules are welded to the chamber for validation purposes (temperature uniformity mapping and pressure tests).
- The piping and air ducts are made entirely from 316L stainless steel with sanitary fittings (tri-clamp ferrules and hygienic flanges).
- Chamber with perfect drainage.
- The equipment body is supported by a base that evenly distributes the floor loads.
- All of the chambers internal surfaces are mechanically polished and then subjected to chemical degreasing, pickling and passivation treatments. Surface finish: ≤ 0.35 micron.
- The unloading-side door hopper has been designed to be completely sealed with the “bio-seal” clean chamber.
- Various fully automatic product unloading options.
We may be small, but we can achieve great things.
Thanks to our customisable after-sales service packages, we offer solutions to suit every need. Choose the one that suits you best!
Customisation is quick and easy
Keep up to date with the latest news from the Last Technology worldand let us steer you towards the most suitable service for you!