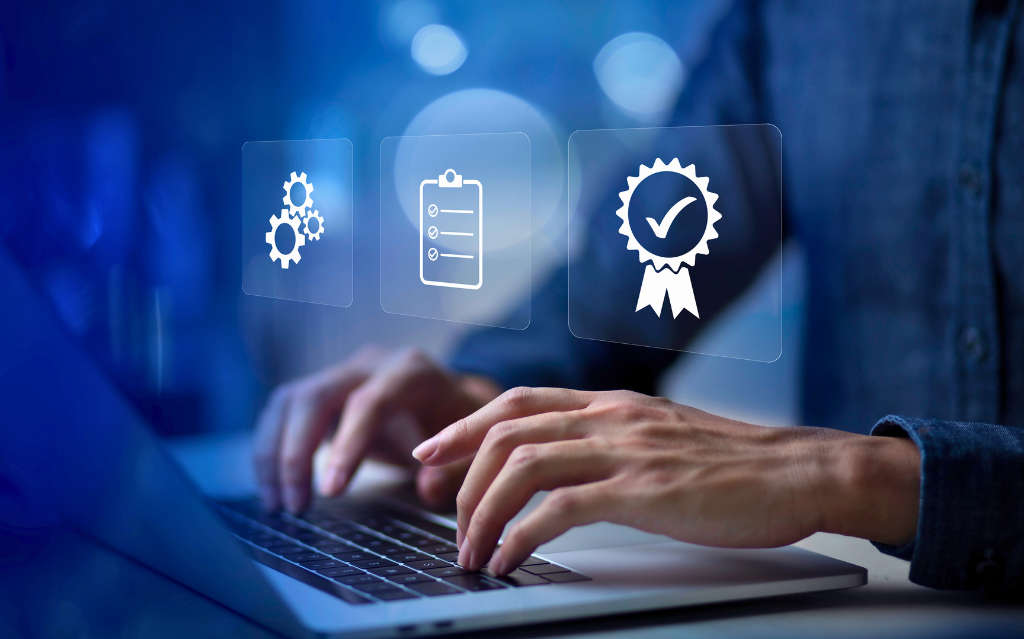
In the pharmaceutical industry, certification of manufacturing processes is not only a guarantee of quality, but an indispensable requirement for operating according to international standards. Patient safety, regulatory compliance and company reputation depend to a large extent on the traceability, validation and reliability of each stage of production. In this article we explore the importance of certifications and their practical impact on efficiency, safety and competitiveness.
Process certification: why it is critical in pharmaceutical manufacturing
In the highly regulated environment of the pharma industry, compliance with regulations such as cGMP (Current Good Manufacturing Practices) is essential to ensure product quality and patient safety. Process certifications-achieved through audits, quality control, and regulatory inspections-establish that every production step, from instrument washing and sterilization to packaging, follows strict and standardized criteria.
Specifically, certified processes enable:
- Complete traceability of operations, which is useful in case of controls or recalls
- Reduction of contamination risks thanks to validated machinery and automated protocols
- Access to international markets, which require compliance with specific regulations (EMA, FDA, WHO, etc.)
- Continuous improvement through constant monitoring of production performance
In addition to quality, certification also directly affects the internal organization, fostering a culture of accountability, documentation and accuracy.
The impact on the choice of machinery and technology
A certified process starts with an informed design and technologies that can guarantee consistent and verifiable performance. Machinery intended for washing, disinfection, sterilization, depyrogenation, decontamination or drying must be designed to meet controllable, repeatable and validable parameters.
LAST Technology, for example, offers customized solutions for the pharmaceutical sector, in which every component-from automated washing cycles to sterilization chambers-is designed to meet the regulatory and technical requirements of international guidelines. Functions such as automatic temperature control, digital document management and real-time traceability systems are now indispensable elements for achieving process validation.
Investing in certifiable machinery also means reducing the time and costs associated with obtaining production permits, accelerating market access and offering partners a concrete guarantee of reliability and compliance.
In an industry where every detail can make a difference, certification of production processes is a key pillar in ensuring safety, quality and efficiency. It is not simply a bureaucratic requirement, but a strategic lever that encompasses every aspect of production activity: from the design of plants to the choice of technologies, to distribution on the global market. With this in mind, focusing on reliable, validatable and customized technologies is the key to building a safer, more transparent and competitive pharmaceutical system.