
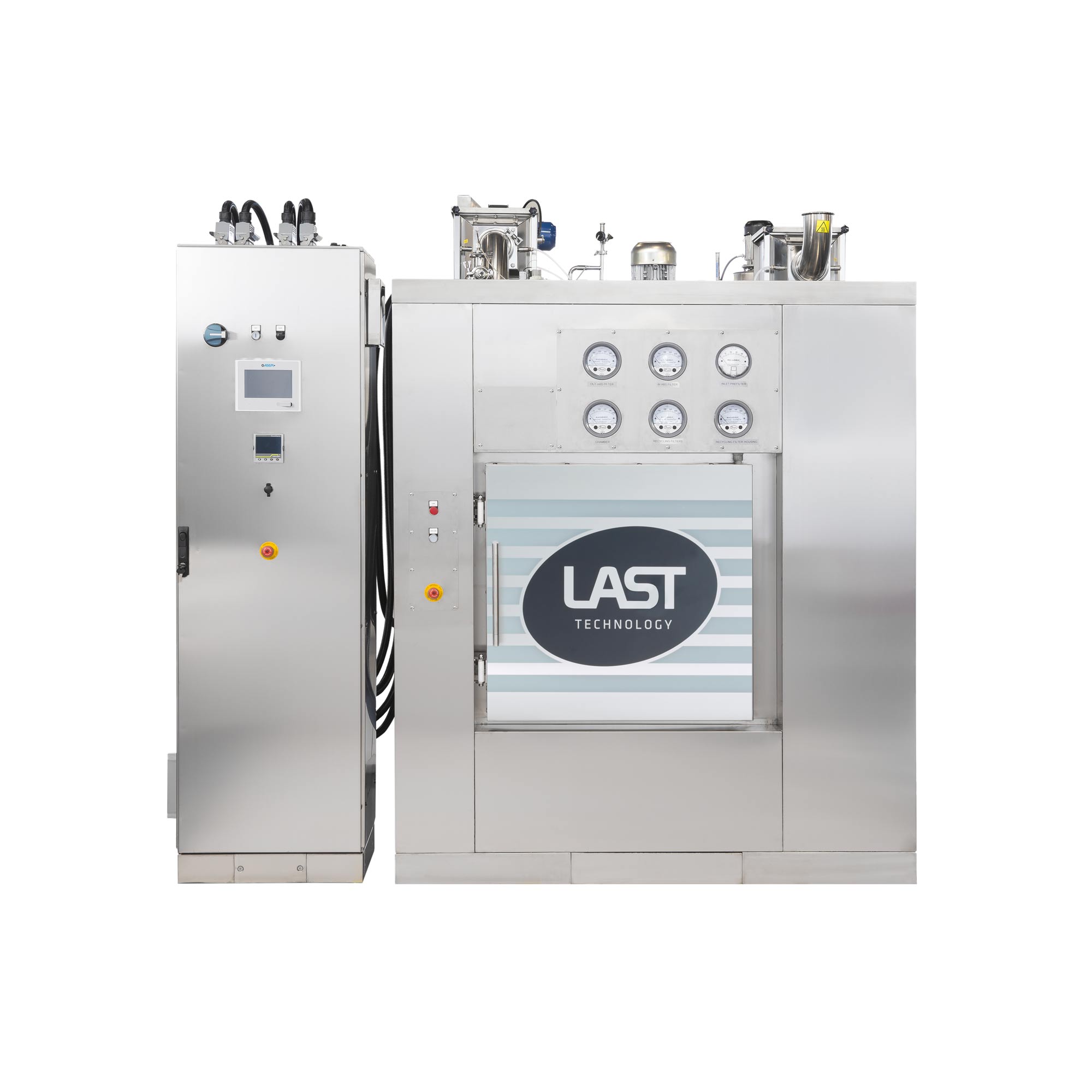
Predefined and “custom” programmes for every need. The equipment process is developed by our Automation Department, according to the current regulations/standards and the type of product being sterilised or depyrogenated. The DHS-series dry heat sterilisers have been designed to be ISO 14664-1-compliant (Class 100 according to US Federal Standard 209 E) up to a temperature of 300°C. Class 100 is guaranteed throughout the entire cycle (heating, sterilisation/depyrogenation and cooling phases). LAST Technology verifies and guarantees these performances during the equipment’s FAT, by sampling the particle content inside the steriliser throughout the cycle (especially during the cooling phase as this is the most critical due to the expansion and retraction of the frames and filters). The system also ensures optimum heat distribution throughout all the sterilisation/depyrogenation phases (temperature deviation below ± 2°C).
- Rectangular sterilisation/depyrogenation chamber and hatches (doors).
- Fully welded one-piece chamber with rounded corners to ensure excellent hygiene levels and facilitate internal surface cleaning.
- The chamber/base is fitted with a cavity to quickly and uniformly heat and cool loads.
- The mechanical construction is resistant to temperatures above 350°C.
- Air is uniformly distributed inside the chamber by means of perforated walls with multi-diameter holes (holes with a bigger diameter towards the bottom and holes with a smaller diameter towards the top).
- The air recirculation and distribution system is installed in the upper part of the steriliser. The heating elements and cooling exchanger are installed concentrically with respect to the impeller of the air recirculation fan.
- The chamber is positioned on a tubular-type base to evenly distribute the weight on the floor.
- The loading trolley-inserting and removing guides are positioned on the bottom of the chamber; they are also height-adjustable.
- Two 1.5” tri-clamp ferrules are welded to the chamber for validation purposes (air particle sampling and temperature uniformity mapping).
- All of the chambers internal surfaces are mechanically polished and then subjected to chemical degreasing, pickling and passivation treatments. Surface finish: ≤ 0.35 micron.
- Above-floor chamber installation.
- Both doors (loading and pick-up side) have been designed to be connected to the walls of the clean chambers (“Bio-seal” interface).
Depyrogenation Oven - Dry heat sterilizers
PHARMA DIVISION
cGMP dry heat steriliZers
The DHS dry heat sterilizers have been designed to class 100 (ISO 5) hot air sterilise and depyrogenate empty glass containers, such as bottles, vials and stainless steel parts. By retaining the dry heat at a temperature of 250-300°C for a controlled period of time, the microorganisms are inactivated and destroyed.
SOLIDS
AIR
250°C – 300°C
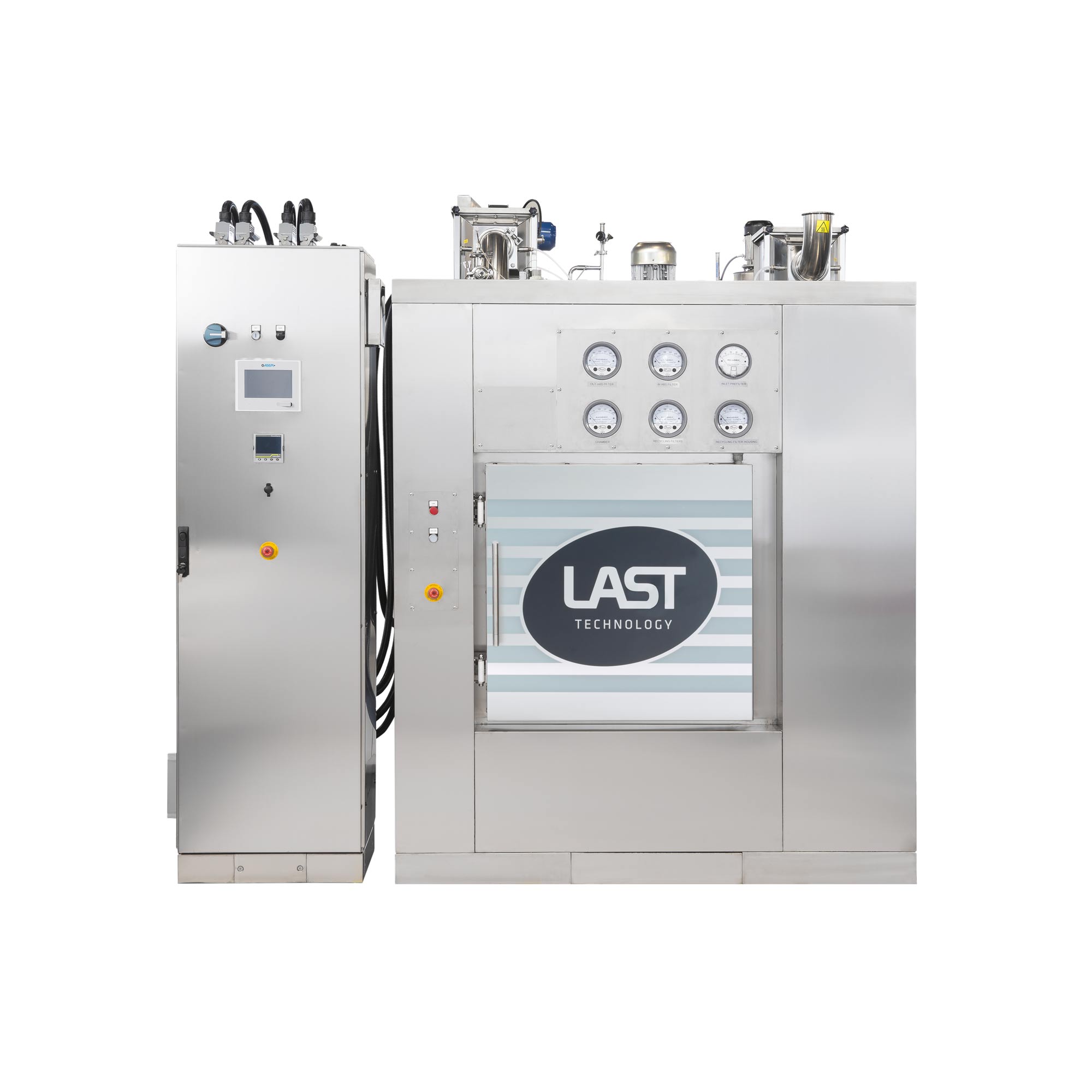
Predefined and “custom” programmes for every need. The equipment process is developed by our Automation Department, according to the current regulations/standards and the type of product being sterilised or depyrogenated. The DHS-series dry heat sterilisers have been designed to be ISO 14664-1-compliant (Class 100 according to US Federal Standard 209 E) up to a temperature of 300°C. Class 100 is guaranteed throughout the entire cycle (heating, sterilisation/depyrogenation and cooling phases). LAST verifies and guarantees these performances during the equipment’s FAT, by sampling the particle content inside the steriliser throughout the cycle (especially during the cooling phase as this is the most critical due to the expansion and retraction of the frames and filters). The system also ensures optimum heat distribution throughout all the sterilisation/depyrogenation phases (temperature deviation below ± 2°C).
- Rectangular sterilisation/depyrogenation chamber and hatches (doors).
- Fully welded one-piece chamber with rounded corners to ensure excellent hygiene levels and facilitate internal surface cleaning.
- The chamber/base is fitted with a cavity to quickly and uniformly heat and cool loads.
- The mechanical construction is resistant to temperatures above 350°C.
- Air is uniformly distributed inside the chamber by means of perforated walls with multi-diameter holes (holes with a bigger diameter towards the bottom and holes with a smaller diameter towards the top).
- The air recirculation and distribution system is installed in the upper part of the steriliser. The heating elements and cooling exchanger are installed concentrically with respect to the impeller of the air recirculation fan.
- The chamber is positioned on a tubular-type base to evenly distribute the weight on the floor.
- The loading trolley-inserting and removing guides are positioned on the bottom of the chamber; they are also height-adjustable.
- Two 1.5” tri-clamp ferrules are welded to the chamber for validation purposes (air particle sampling and temperature uniformity mapping).
- All of the chambers internal surfaces are mechanically polished and then subjected to chemical degreasing, pickling and passivation treatments. Surface finish: ≤ 0.35 micron.
- Above-floor chamber installation.
- Both doors (loading and pick-up side) have been designed to be connected to the walls of the clean chambers (“Bio-seal” interface).
Dry heat sterilisers
PHARMA DIVISION
cGMP dry heat sterilisers
The DHS dry heat sterilisers have been designed to class 100 (ISO 5) hot air sterilise and depyrogenate empty glass containers, such as bottles, vials and stainless steel parts. By retaining the dry heat at a temperature of 250-300°C for a controlled period of time, the microorganisms are inactivated and destroyed.
SOLIDS
AIR
250°C – 300°C
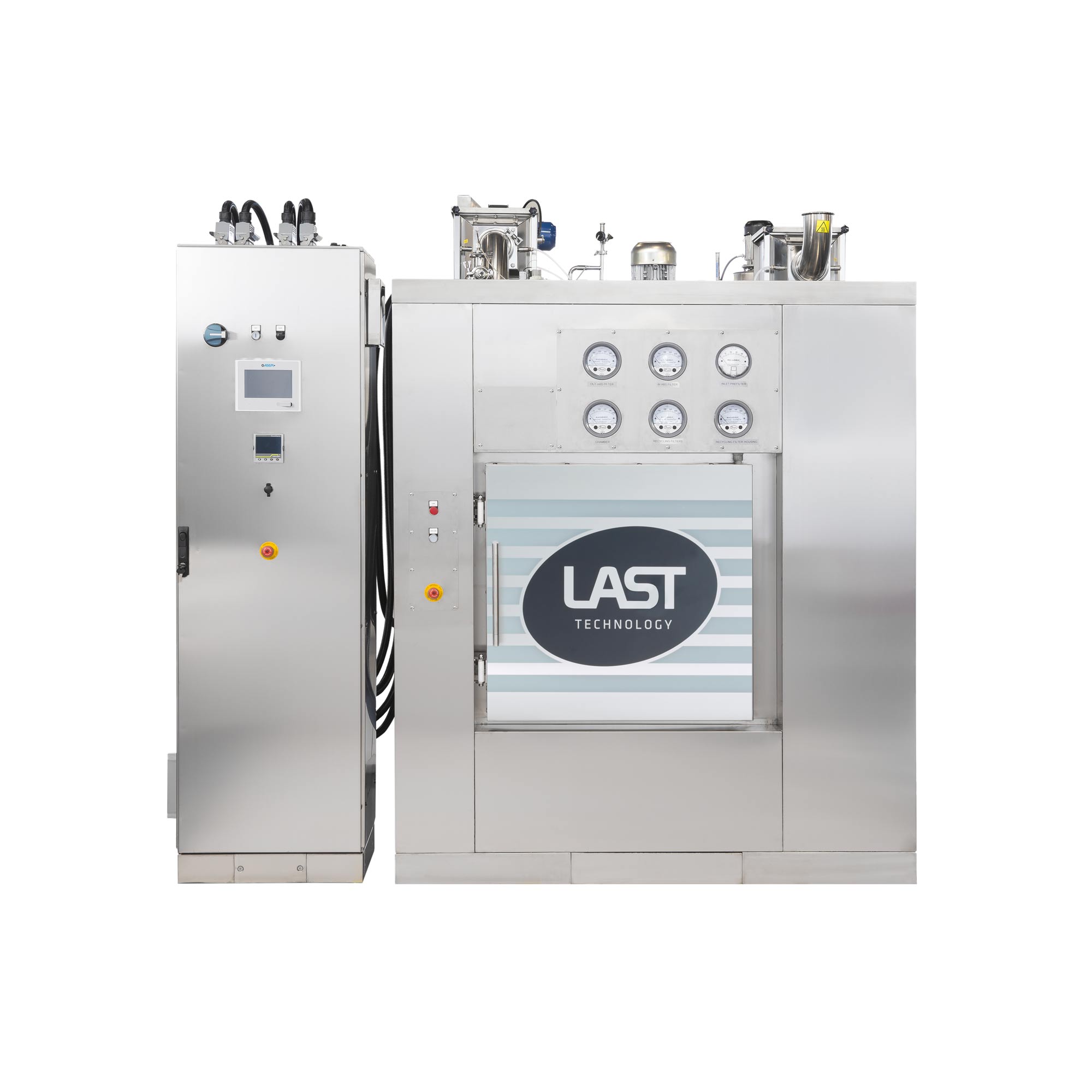
Dry heat sterilisers
PHARMA DIVISION
cGMP dry heat sterilisers
The DHS dry heat sterilisers have been designed to class 100 (ISO 5) hot air sterilise and depyrogenate empty glass containers, such as bottles, vials and stainless steel parts. By retaining the dry heat at a temperature of 250-300°C for a controlled period of time, the microorganisms are inactivated and destroyed.
SOLIDS
AIR
250°C – 300°C
Predefined and “custom” programmes for every need. The equipment process is developed by our Automation Department, according to the current regulations/standards and the type of product being sterilised or depyrogenated. The DHS-series dry heat sterilisers have been designed to be ISO 14664-1-compliant (Class 100 according to US Federal Standard 209 E) up to a temperature of 300°C. Class 100 is guaranteed throughout the entire cycle (heating, sterilisation/depyrogenation and cooling phases). LAST verifies and guarantees these performances during the equipment’s FAT, by sampling the particle content inside the steriliser throughout the cycle (especially during the cooling phase as this is the most critical due to the expansion and retraction of the frames and filters). The system also ensures optimum heat distribution throughout all the sterilisation/depyrogenation phases (temperature deviation below ± 2°C).
- Rectangular sterilisation/depyrogenation chamber and hatches (doors).
- Fully welded one-piece chamber with rounded corners to ensure excellent hygiene levels and facilitate internal surface cleaning.
- The chamber/base is fitted with a cavity to quickly and uniformly heat and cool loads.
- The mechanical construction is resistant to temperatures above 350°C.
- Air is uniformly distributed inside the chamber by means of perforated walls with multi-diameter holes (holes with a bigger diameter towards the bottom and holes with a smaller diameter towards the top).
- The air recirculation and distribution system is installed in the upper part of the steriliser. The heating elements and cooling exchanger are installed concentrically with respect to the impeller of the air recirculation fan.
- The chamber is positioned on a tubular-type base to evenly distribute the weight on the floor.
- The loading trolley-inserting and removing guides are positioned on the bottom of the chamber; they are also height-adjustable.
- Two 1.5” tri-clamp ferrules are welded to the chamber for validation purposes (air particle sampling and temperature uniformity mapping).
- All of the chambers internal surfaces are mechanically polished and then subjected to chemical degreasing, pickling and passivation treatments. Surface finish: ≤ 0.35 micron.
- Above-floor chamber installation.
- Both doors (loading and pick-up side) have been designed to be connected to the walls of the clean chambers (“Bio-seal” interface).
We may be small, but we can achieve great things.
Thanks to our customizable after-sales service packages, we offer solutions to suit every need. Choose the one that suits you best!
Customization is quick and easy
Keep up to date with the latest news from the LAST Technology world and let us steer you towards the most suitable service for you!