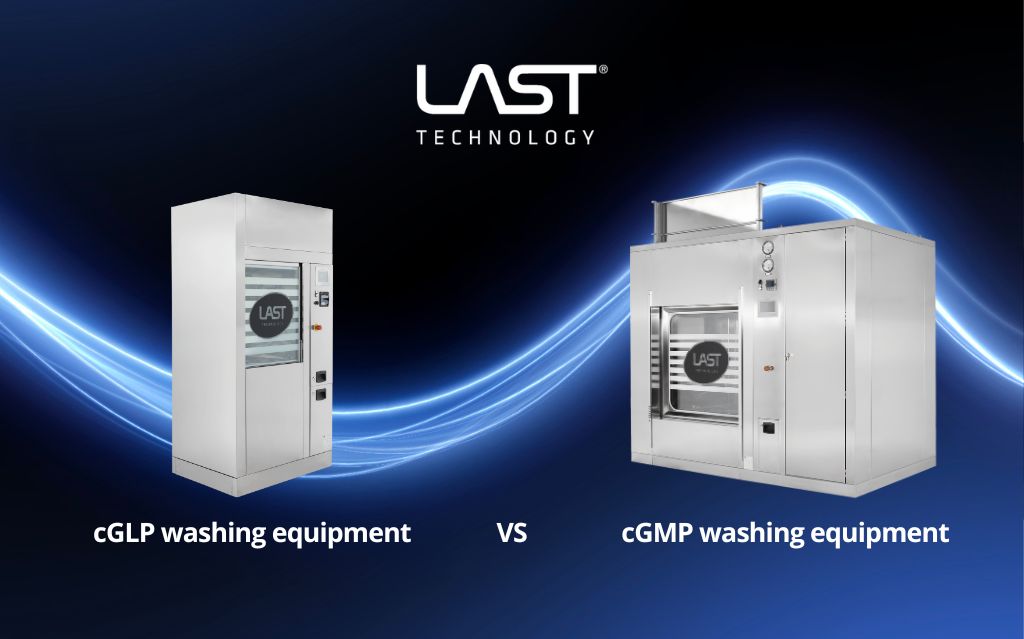
In the pharmaceutical industry, where precision and safety are crucial, hygiene and cleanliness play a key role. Washing equipment is an essential element in the entire production process, ensuring that the tools and equipment used are free of contaminants and meet the quality standards required by international regulations.
However, all machinery is not the same, quite the contrary. Let’s try to shed some light on two acronyms that refer to two different washing equipment: GMP and GLP. We will go over the distinguishing characteristics of each and the importance of choosing the equipment best suited to each customer’s specific needs.
How does GMP washing equipment differ from GLP?
The main differences between GMP (Good Manufacturing Practice) and GLP (Good Laboratory Practice) washing equipment are in design, flow rate regulations, documentation, and process automation. Here is an overview of the key differences:
- Mechanical design and flow rate regulations
- GMP washing equipment: They use FDA-approved seals and connections, fully drainable AISI 316L stainless steel piping. Design follows GAMP 5 regulations, and internal trolleys are designed for process components.
- GLP washing equipment: They use standard components with a combination of rigid and flexible piping, threaded connections, and different types of gaskets. Not all piping is fully drainable and the design does not comply with GAMP 5. Internal carts are designed for all laboratory materials.
- Documentation
- GMP washing equipment: Documentation is complete for qualification and complies with GAMP 5.
- GLP washing equipment: Documentation is based on the product catalog and is not fully compliant with GAMP 5.
- Software, automation and process control
- GMP washing equipment: Use automation with PLC + IPC (FDA 21 CFR Part 11 compliant).
- GLP washing equipment: Use automation with PLC + HMI, dedicated to laboratory products, without SCADA availability.
How to choose between the two?
The correct selection of washing equipment can significantly affect the efficiency, safety, and quality of production processes and research. Each customer has special requirements that must be met to ensure full compliance with quality and safety regulations.
Equipment selection must take into account factors such as the type of materials to be washed, the frequency and complexity of washing cycles, and specific cleaning and sterilization requirements. In addition, considerations such as compliance with industry regulations, required documentation, and integration with other production processes must be carefully evaluated.
Opting for the most appropriate washing equipment is essential to ensure maximum operational efficiency, personnel safety and regulatory compliance, thus contributing to the success of both pharmaceutical and laboratory operations. At LAST Technology we offer our advice, even before our machines, to help you make the best choice.